IIR establishes a working group to promote refrigeration safety
While standards have helped the refrigeration industry to improve and set safety requirements, the International Institute of Refrigeration is proposing a working group to enhance refrigeration safety.
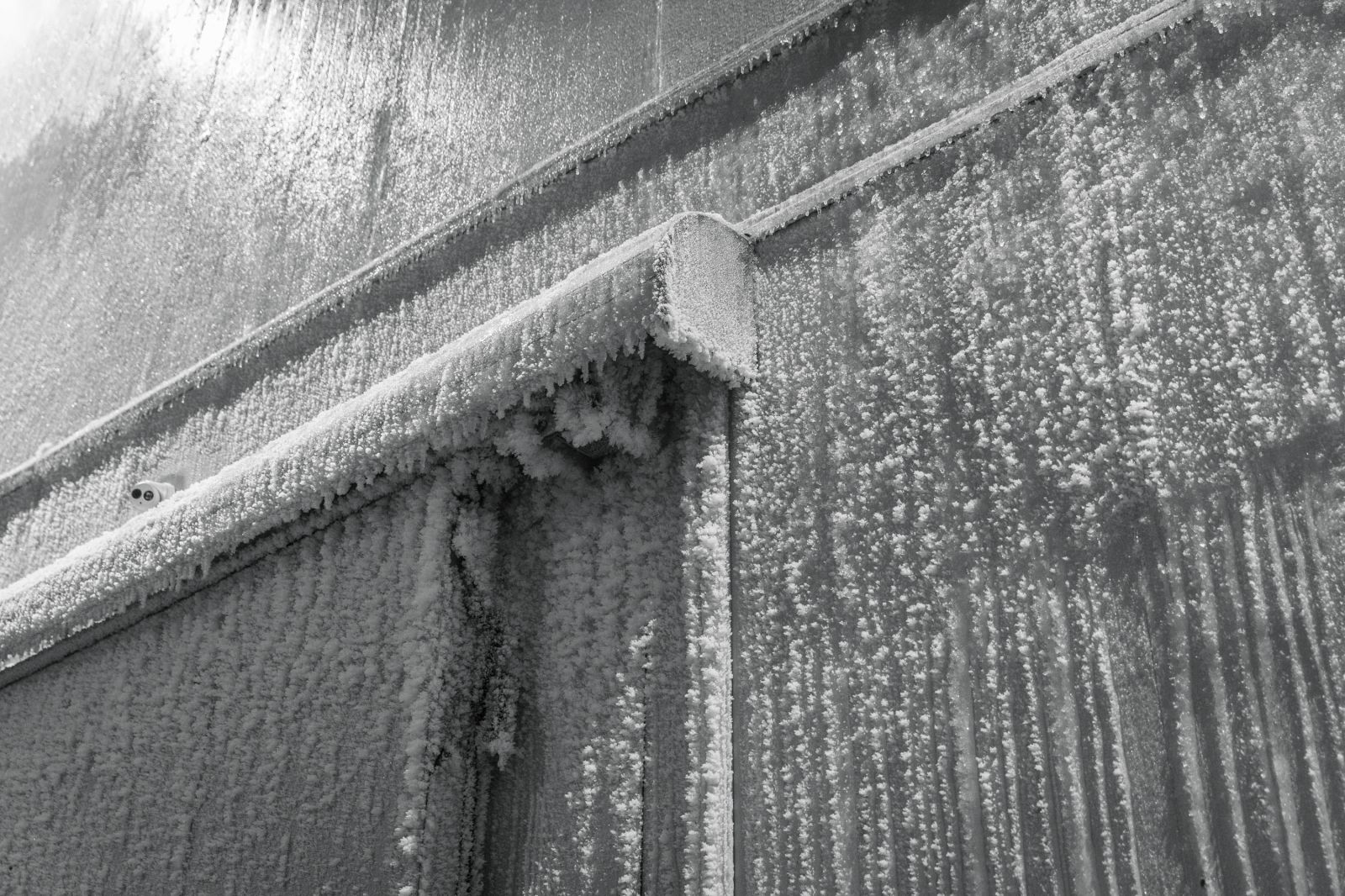
Over the last 150 years, we have learned how to use a number of different refrigerants. The first refrigerants were ammonia, ethers, methyl chloride, air and CO2. Later, hydrocarbons emerged, and in 1930s we saw the first series of CFCs, mainly R-11 and R-12, emerging on the market, followed by HCFCs such as R-22 and R-502. Of those refrigerants that preceded CFCs, only ammonia remained on the mainstream market, with CO2 and the hydrocarbons disappearing. Ammonia was used in large industrial systems in many countries because it was very energy efficient.
Over the years, accidents happened when working with these refrigerants, but these showed engineers and technicians how to design risk-free systems and work safely with the different fluids. Standards and guidelines helped the industry to set safety requirements.
In the research and development undertaken in order to find an alternative to refrigerants with a high global-warming potential (GWP), the chemical and the industry has found new solutions with low or practically no GWP. However, these solutions come with a price – they are flammable and in some cases toxic. Other refrigerants produce toxic by-products that cannot be broken down by natural processes.
These new refrigerants require new skills from engineers and technicians. The evolution of higher standards must be accelerated if the industry is to meet the goals set by the politicians. Knowledge must be collected through ongoing experience.
For these reasons, we are proposing the formation of a new working group that will speed up the process of knowledge accumulation from the lessons we learn the hard way from experience. The outcome of the working group will be a report describing what we have understood regarding the risks and safety requirements of various refrigerants. The report will need to be updated on a regular basis in order to maintain its relevance and to disseminate the most recent learnings.
Who can participate?
In principle, everybody can feed information to the group. All reports of accidents, their causes and the preventative measures taken to avoid them will be evaluated, compared and categorised. While we prefer participants to be members of IIR, anyone can attend the meetings, including those in fields that do not have the financial means to join IIR. Translations of press stories reporting local incidents locally will provide information that we would otherwise never hear about.
How to get in contact
Information can be sent by e-mail to Alexander Cohr Pachai, Technology Manager at Sabroe Factory for Johnson Controls and Chair of the working group, who will lead the work. All relevant information is welcome. Please clearly state the place and date of the accident and if possible the type of refrigerant used. Press reports are not always accurate, so please verify the information contained in them with the local rescue centre. Alexander Cohr Pachai: [email protected].
Alexander Cohr Pachai, Technology Manager at Johnson Controls (and Chair of IIR working group)
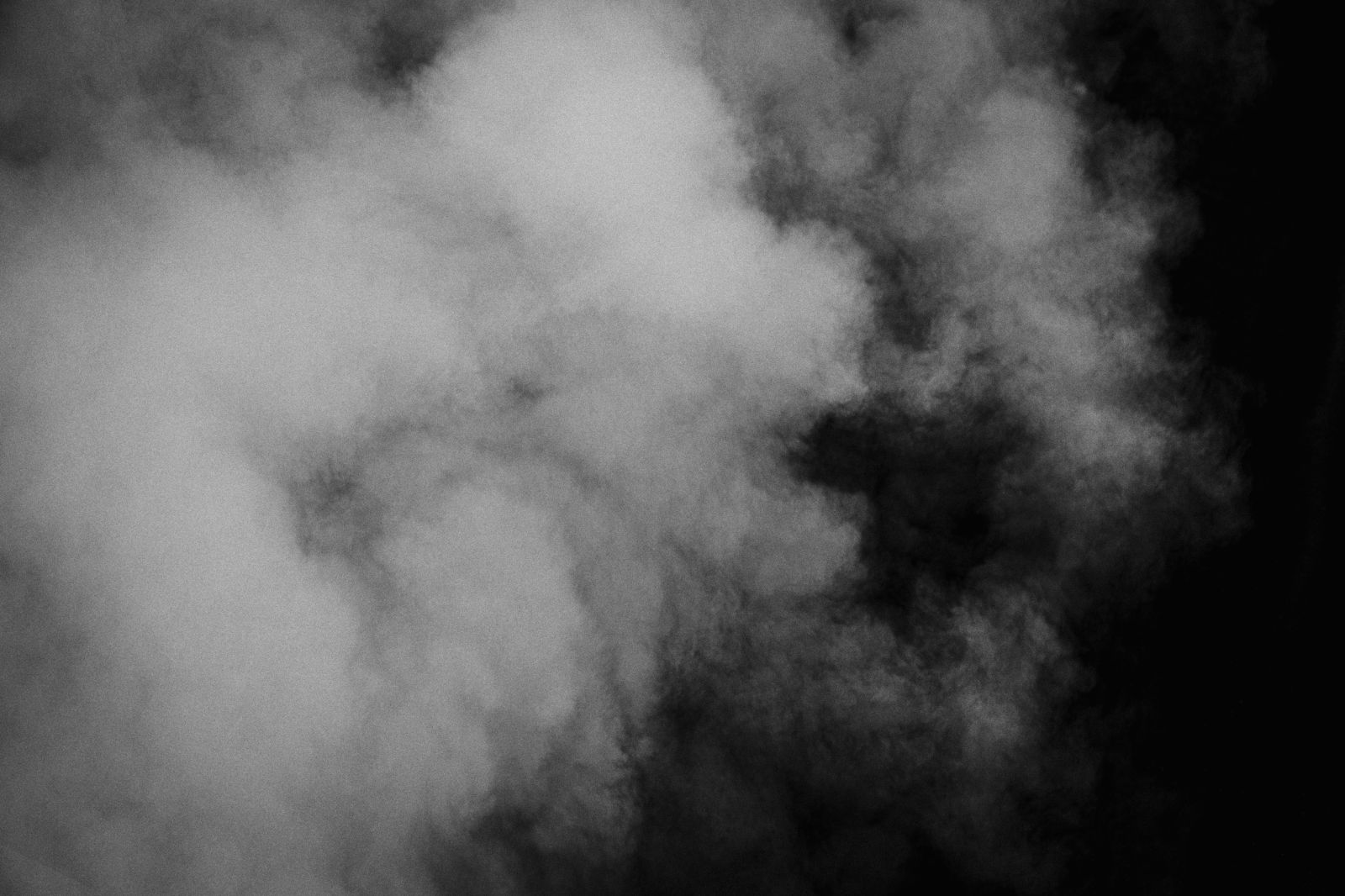
Meet our Partners
Everyone Benefits from Smart Cooperation
Vahterus tests its products at a steam laboratory installed in the Naantali power plant of Turun Seudun Energiantuotanto (TSE), an energy production company in the Turku region. The test laboratory, which has exceptionally high capacity, is used to study the qualities of Vahterus steam condensers for product development purposes.
The International Institute of Refrigeration (IIR)
While standards have helped the refrigeration industry to improve and set safety requirements, the International Institute of Refrigeration is proposing a working group to enhance refrigeration safety.
Export Credit Agency Finnvera
Did you know that, with the help of the right financing options, an export business can offer buyers credit at competitive rates? These options include bills of exchange and deferred letters of credit.